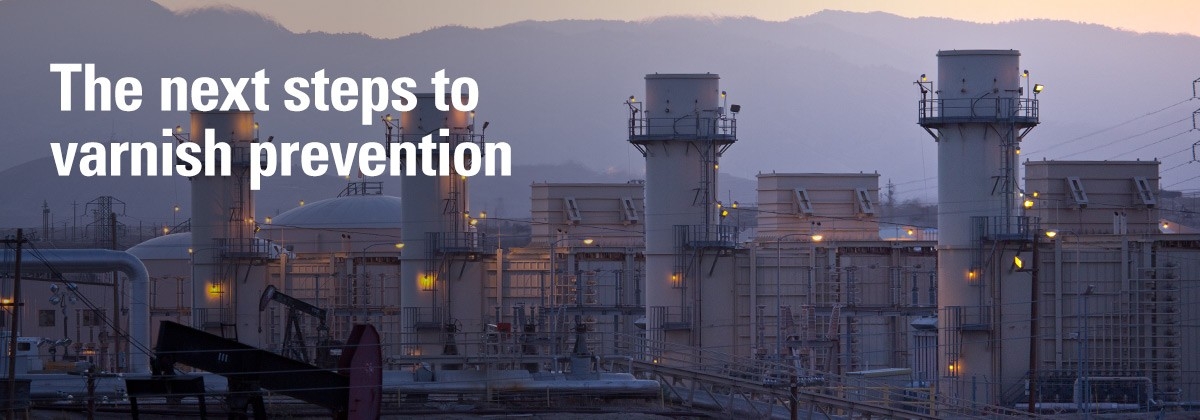
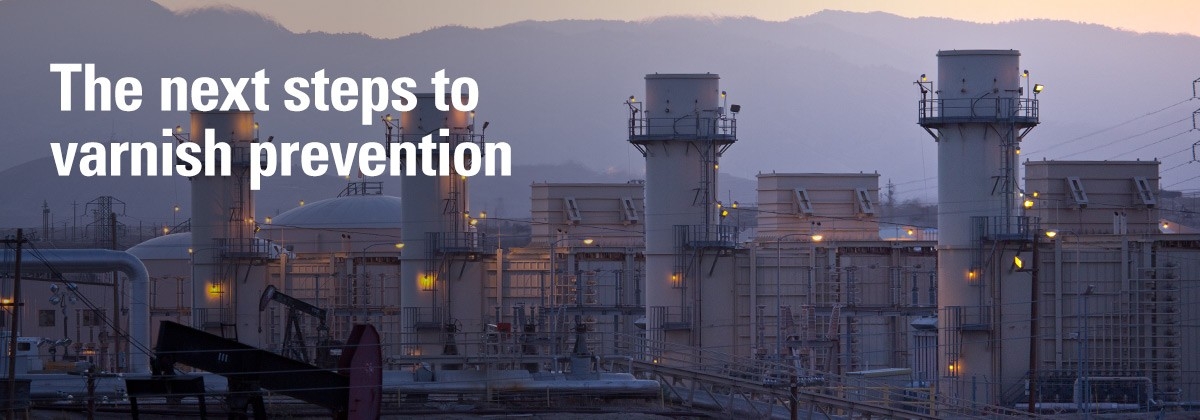
As you’re preparing for the shift towards a more proactive approach to preventing turbine varnish-related issues, we’ve anticipated some of the questions you might have and provided answers to help guide you through the process.
Yes. And the treatment—or removal—of varnish depends on the type of varnish that has formed and how it was generated in the first place.
There are several examples of costs and fines associated with varnish buildup in combustion turbines. The costs may include chemical treatments, parts replacement for plugged filters, and the actual labor costs to replace those filters. Additionally, there may be fines and lost revenue for turbine trip events or failures to start.
There are several laboratories that perform tests to identify the varnish precursors in the oil before varnish forms in the turbine systems. Some of these include membrane filter patch tests or colorimeter tests.
Effective, premium varnish-mitigating products are carefully formulated with a specific blend of base oils and the right additive system which synergistically provides varnish mitigation performance. This starts with oxidation resistance and includes improved deposit control.
Keeping the oil isolated from contamination goes beyond just keeping other fluids out. It also means ensuring that you’re only using clean storage and transfer equipment. Also, buying certified clean oil that meets the OEM’s oil cleanliness specification is key to extending oil and equipment life—as is keeping it free of particulate contamination.
The equipment will be unavailable for 1 or 2 weeks as a result of the switch, which means lost revenue. This drives most users to look for the fastest turnaround, but unfortunately, many don’t realize that varnish removal is not a fast process. To do it properly and have a longer-lasting effect on the equipment means taking the time to do it right before bringing things back on line.
Varnish formation is initiated by high temperatures. The rate and type of varnish is dependent upon the oil film thickness (as in, the amount of oil) and time exposed to the heat. The amount of contaminants present is also a factor. Initially, varnish is suspended in the oil until it either agglomerates to a size that is no longer soluble or the oil is cooled enough that it loses enough solubility to help sludge, varnish, lacquer, and more.
Ready to stop varnish now?
Request a Chevron Lubrication specialist to help you assess your varnish potential and show you how to mitigate varnish in your equipment.